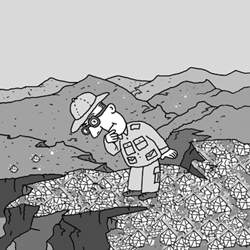
To see a world in a grain of sand
- William Blake, Auguries of Innocence
The quest for quality films is at the forefront of nanotechnology research. The distinguishing characteristic of these films is their thinness - they are built of one or several layers of molecules, where each layer may range in thickness from just a few nanometers to several microns.
Current applications include computer and other electronic chips, sensors, flame-retardant films and liquid crystal displays (which alone have an estimated market of nearly $12 billion).
Key challenges in this field include the intro-duction of better characterization and quality control tools with which to analyze these tiny materials, and the development of films with enhanced organization, thermostability and complexity.
Thin films on a scale
Time equals money. But so does weight - when it comes to the films used in computers and optical telecommunications. Shaving off pounds from these devices could mean huge benefits for microelectronics as well as for satellites or spacecraft, where launching costs around $50,000 per kilogram (2.2 pounds).
A new recruit to the Institute, Dr. Milko van der Boom of the Organic Chemistry Department, is working to create thin films with such desirable qualities as low weight and long-term thermostability. He is targeting an “all-organic” product, which he hopes will replace today’s inorganic materials. The rationale is simple. Organic films would be much easier to modify, offering far better, cheaper devices that could even be introduced into home appliances, revolutionizing the electronics industry.
The challenges of creating these films, however, are considerable - from effectively integrating organic molecules into thin films, to creating films that are thick enough to efficiently convey the light signal.
To address these challenges, Van der Boom and groups led by Prof. Tobin J. Marks and Prof. Pulak Dutta at Northwestern University have created a novel bottom-up growth method. The teams begin by producing custom-designed organic molecules, which they then integrate into the film, building it up layer by layer (each layer is only 2.5 nanometers thick).
They had to “trick” nature to do so, organizing the molecules in a novel arrangement in which the molecules are all aligned in one direction. “Nature prefers a random orientation,” says Van der Boom.
Another innovation is the introduction of polymers that help to organize the films, creating smoother materials. Using this approach, the teams have created highly organized films consisting of 100 layers - a marked improvement over the average 10-layer films achieved to date. The team has recently created the first prototype electro-optic modulators based on these films.
Beneficial defects
Just as gourmet chefs chop carrots and onions into admirably fine slices, scientists working with nano-materials hope to create ever-thinner crystals - films so thin they can't be seen by the naked eye. The goal: to determine at what point these films exhibit one of the remarkable quirks of nanochemistry - taking on properties that are dramatically different from those of their original crystals.
The stumbling block in this endeavor is the films' tendency to collapse at a thickness of 5 microns (five millionths of a meter). Scientists have tried stabilizing films by placing them on various supporting surfaces, however, this process often affects their properties.
Targeting this challenge, Dr. Igor Lubomirsky of the Materials and Interfaces Department is studying an unusual form of freestanding films - also known as substrate-free films - in which the films are supported only along their edges, like drums.
Working with Vera Lyahovitsky of the same department, Lubomirsky has developed a production technique that allows control of grain size, shape and dispersion - all key mechanical factors in achieving film stability. He is also developing a new characterization technique designed to uncover the precise link between the way a film is prepared and its resulting properties, which might advance the production of new films with predictable, hence controllable, properties.
Lubomirsky has applied his technique to create nanofilms from a variety of materials, one of which was recently described in Europhysics Letters. The grains in these films are significantly smaller than those in the original material, resulting in an increased surface-to-volume ratio, richer interactions between neighboring grains and a much higher bonding energy. This in turn leads to new optical, mechanical and conductivity properties and even to new types of defects. “Some of these qualities, even those perceived as defects, may turn out to be very useful,” says Lubomirsky.
Future nanocrystalline films might be used to produce tiny, highly efficient fuel cells, advanced infrared detectors and high-frequency microelectronics. Other films might find their way into medical applications, such as microsensors or microinjectors that would be positioned within the body, delivering medications directly on target.
Why choose a smaller diamond
Diamonds are far more than sparkling gems meant to complete an evening gown. Roughly 80 percent of the diamonds mined annually are used for industrial applications - all designed around the stone’s unique chemical and mechanical properties, which have fascinated scientists for centuries.
Made of carbon, diamonds are one of the strongest materials known, have the highest thermal conductivity in nature, and are chemically inert and optically transparent. Their mechanical strength makes them an obvious choice for wear-resistant coatings used in cutting and polishing tools, eyeglasses, computer chips and blades used in high-precision surgery.
Synthetic diamonds lead the way in most of these applications. They are cheaper and far easier to work with than natural diamonds. Yet despite significant advances in production since their discovery in the 1950s (see box), key challenges remain. Two of these were recently tackled by Weizmann Institute researchers.
One technique for producing synthetic diamonds, known as chemical vapor deposition (CVD), involves a gas-phase reaction in which small diamonds are deposited onto a solid surface. These diamonds serve as “seeds” that promote nucleation centers around which individual crystals form and eventually connect to create a closed layer. Attempts to commercially produce high-quality CVD films are hindered by a painfully slow growth rate and the need for extremely high deposition temperatures.
Aiming to enhance the process, Prof. Yehiam Prior of the Institute’s Chemical Physics Department replaced the traditional diamond particles used for nucleation with particles half their size - around 50 nanometers. This subtle change in protocol resulted in significantly improved production rates and quality, making possible the synthesis of uniform films less than 500 nanometers thick. It also reduced the temperatures necessary by roughly 40%. “The minuscule size of these nucleating particles makes the ratio of their surface area to volume unusually large, promoting better bonding and thus better, more uniform films,” Prior explains.
From nature’s depths to a factory production line
In 1796 British chemist Smithson Tennant established that diamonds are a crystalline form of carbon (according to some reports, burning his wife’s diamonds to do so) - the same material of which coal, graphite and other combustible materials are made.
The race to produce synthetic diamonds began, but it would be more than 150 years before the secret of converting graphite into the coveted diamond was discovered. The “recipe” called for temperatures of 1,400 degrees C and pressures of over 55,000 atmospheres. The recent development of CVD, characterized by much lower temperature and pressure production levels, may advance entirely new applications, including hip or other body part replacements, made possible due to the chemical inertness of diamonds.
The effect of the defect
Iris Visoly-Fisher knew exactly what she wanted to work on when starting her Ph.D - to follow up on a hunch she had that defects in a certain material used in solar cells would actually improve their performance.
But something was bugging her. She couldn’t understand why so few people were working on this topic. “It seemed so clear that something was up, but there was virtually no literature about it,” she says.
She soon found out why. The technical difficulties in examining this puzzle were significant. To effectively tackle the problem, she would need to figure out how to zoom in on solar cell performance at the nanoscopic scale.
An unexplained finding from years earlier was what had triggered this headache of a challenge. Most commercial solar cells are made of single crystal semiconductors, such as silicon, Visoly-Fisher explains. But researchers had been looking around for alternative materials for a while, since silicon’s manufacture costs are high. Then, nearly 15 years ago, a finding came up that was out of sync with all predictions. Certain solar cells made of polycrystalline (multi-grained) films were systematically outperforming their counterpart single crystal cells.
Nobody understood why. Scientists working to improve solar cells had traditionally shied away from multi-grain films since they contained numerous structural defects - a property believed to impair the light conversion process.
“In examining and reexamining the multi-grained films that had proven so successful, we could come up with only a key difference between them and the single crystal films: the presence of a leading defect, known as the grain boundary defect,” says Visoly-Fisher, who performed the study under the guidance of Prof. David Cahen of the Institute’s Materials and Interfaces Department, in collaboration with Dr. Sidney Cohen of the Chemical Research Support.
The team decided to find a way of studying the electrical properties of a single defect - in other words, the meeting point between two of these microscopic grains. Only after combining 3 different high-resolution imaging techniques did they have an irrefutable answer: Contrary to earlier notions, grain boundary defects significantly enhance the efficiency of certain solar cells.
As the Institute team has now shown, the grain boundaries improve the solar cell’s light-to-electricity conversion because they provide a path where free electrons in the semiconductor are efficiently collected and channeled.
“The grain boundaries essentially function as a freeway for electrons to exit, without traffic lights or roundabouts,” says Prof. Cahen. “This finding offers a promising direction for improving solar cell performance while cutting production costs.”
Going magnetic
When Itai Carmeli first came to his Ph.D. adviser with his results, he was gently told to get back to work. “I told him there was no such physics,” recalls a smiling Prof. Ron Naaman of the Institute’s Department of Chemical Physics. “A year later he was back - with similar findings.”
Carmeli had been tinkering around with organic molecules, which he used to create extremely thin, single-layered films on a gold substrate. The surprise was that the films were behaving like a powerful magnet. There are different types of magnets, Naaman explains, from the common fridge magnets we all played with as kids, that always display magnetic behavior; to temporary magnets such as paperclips and nails, which only work when exposed to a strong magnetic field; to magnets powered by an electric current. Nearly all of these contain one or more components with magnetic properties. The twist in our case was that our films lacked any magnetic materials.
In their study, recently published in Physical Review Letters and the Journal of Chemical Physics, the Institute team experimented with films made of three types of organic molecules. The molecules each had a positive and negative pole, and they were tightly packed, such that their negative poles faced the gold substrate, while their positive poles faced away.
And this, says Naaman, might have been the trick: while opposite charges are known to attract, like charges repel, particularly when in close proximity on the surface of the film. The team - which included physicist Prof. Zeev Vager and materials scientists Prof. Shimon Reich and Dr. Gregory Leitus - believes that this repulsion force causes electrons to flow from the gold substrate to neutralize charged sites on the molecules, in an attempt to stabilize the system. This extremely thin layer of electrons in turn induces an electric current - forming a leading type of magnet dubbed an electromagnet (see box).
“We believe that the electrons are behaving as if in a co-op,” says Vager. “Electrons usually orbit in small circles, around individual molecules; but in this case they may be orbiting domains containing hundreds of thousand of molecules in the film, creating an electric current that transforms the system into a powerful magnet. Films of this sort might feature in electromagnets used in futuristic high-density discs and other electronics.”
Magnetic moments
Birds do it, bees do it, so do whales, salmon and, according to a new study, even Caribbean spiny lobsters - all use the earth’s magnetic field as a navigating compass.
Magnetism was first discovered by the ancient Greeks and Chinese. Experimenting with the materials of their natural environment, they found that certain rare stones, called lodestones, attract small pieces of iron. Adding to their “magic,” these stones were found to always point in a north-south direction when suspended on a string. They quickly became invaluable to navigators, fortune-tellers and builders.
During the 13th century Frenchman Pierre de Maricourt discovered that magnets had two magnetic poles - north and south - and in the 1600s, England’s Sir William Gilbert concluded that Earth itself is a giant magnet, with north and south poles - which explains the wonder of animal migration treks.
The 1800s saw the first connection made between electricity and magnetism, when Danish physicist Hans Christian discovered that running an electric current through a wire creates a magnetic field - a phenomenon that quickly became known as electromagnetism. And today, this form of magnetism is everywhere - used in designing the electric motors in refrigerators, washing machines and racecars; the read/write heads of discs and videotape players, and far more.
A mismatch made in heaven
Size is everything… when it comes to materials science. For instance, the properties of crystals smaller than roughly 10 nanometers can be altered by merely changing their dimensions. This phenomenon, known as the quantum size effect, makes it possible to derive materials with dramatically different properties from chemically identical compounds.
Researchers at the Institute’s Materials and Interfaces Department achieved an important step toward this aim using a technique called electrodeposition. Prof. Gary Hodes, Prof. Israel Rubinstein and then doctoral student Yuval Golan laid down crystals of the semiconductor cadmium selenide, each measuring four to five nanometers, onto a gold substrate. The crystals were found to be oriented in a uniform manner. This configuration, which is highly beneficial for controlling semiconductor properties, occurs because the atoms of the cadmium selenide crystals tend to align themselves with the atoms in the surface layer of the gold substrate.
But then the researchers discovered a paradoxical fact: the match had a slight imperfection, and whereas uniform configuration generally improves the control of semiconductor properties, in this case the mismatch allowed for the precise control of crystal size.
It turned out that the gold substrate “stretches” the growing crystal in an attempt to minimize the mismatch, creating a strain within the crystal that eventually causes it to stop growing altogether. By fine-tuning the mismatch the scientists were able to control when the crystal would stop growing, in other words, its size. They showed that by adding small amounts of a material called tellurium they could control the degree of mismatch, thus producing uniformly oriented crystals of varying sizes. Recent results have shown that not only the size of crystals but also their shape and phase can be controlled in this manner.